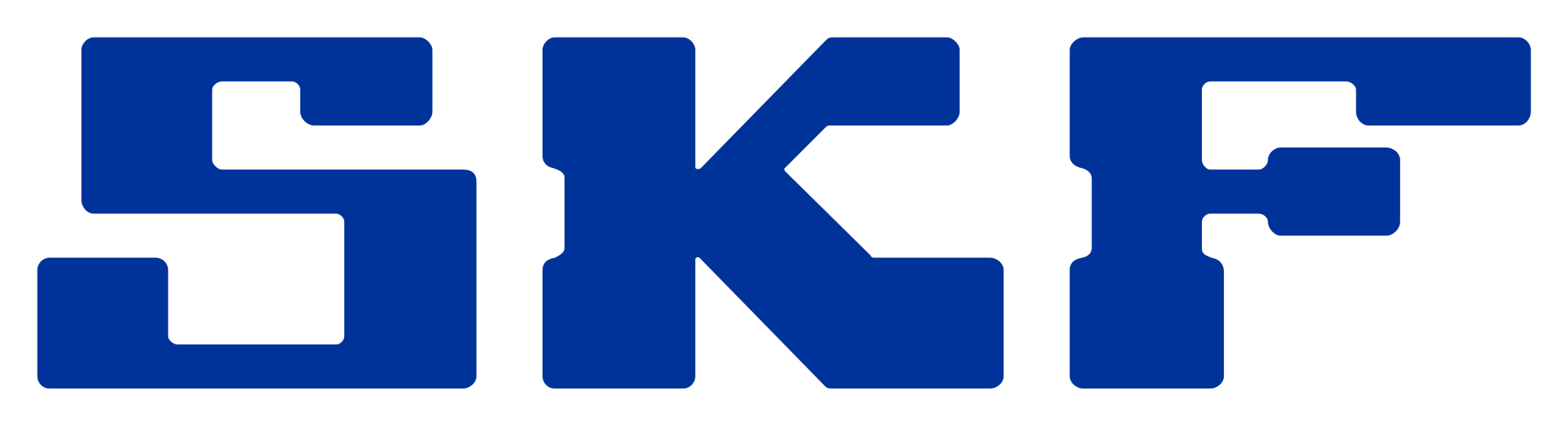
- Customer:Â SKF Technologies India Pvt Ltd.
- Country: India
- Industry:Â Electronics
- Solution:Â Moldex3D Advanced
- View PDF Version
Executive Summary
Every industry has its unique challenges, but virtually all industries share the goals of increased machine uptime, reduced maintenance, improved safety, energy savings and lower total cost of ownership. With expertise in a wide range of disciplines and decades of experience as a technical partner to both equipment manufacturers and end users in every major industry, SKF is delivering not just products but total integrated solutions that help our customers achieve their goals.
The SKF sensor unit in this case includes electronics that need adequate sealing mainly for preventing liquid ingress and mechanical protection. This can be achieved by potting and over molding. The project involves analyzing the over molding of electronics, connectors and cable with printed circuit board (PCB) material as inserts.
Challenges
- To reduce design iteration and prototyping times.
- Identify the defects and correlate the simulation results with actual product failures for design optimization.
- Reduce product development cycle time.
Solutions
Moldex3D Designer and Project helped to create BLM mesh and run simulation successfully. Moldex3D technical support team helped to explore the tool and fix the problems whenever required in minimum time. As SKF has inserts with small electronic components, cable, connector’s etc., achieving good quality mesh was a big challenge. This was achieved using BLM mesh tool as recommended by Moldex3D team.
Benefits
- Optimized the process parameters.
- Identified defects and suggested improvement with respect to design modification and process settings.
- The simulation results helped to investigate the reason for product failure.
Case Study
In the first phase, the objective was to carry out low pressure over molding simulation for single cavity molding. With current process setting identification of design and process defect was one of the main requirements. The observation must be made to find correlation with the existing manufactured part. Phase 2 objective was to realize a rheology over molding study to check the feasibility of molding 2 parts of the same product and define the best position of the injection point, best runner and gate design and dimension of cooling circuit. At the same time, the defect identified in the 1st phase must also be fixed.
The technical centre of SKF used Moldex3D Advanced solution to simulate the molding scenario of the original design. The meshing issue of the small electronic component and cavity was solved by BLM meshing. Through Moldex3D simulation results, they found filling issues in some regions on the part due to the gate location. There was also flow hesitation in thin wall areas. In addition, SKF was able to identify the internal residual stresses on the electronics during molding process. Finally they were able to optimize the process parameters to get the best cycle time and operate at the lowest possible pressure.
There was a design change in the gate type and location of the 2-cavity mold design. The runner system dimension and design was also changed respectively taking into account the defect observed in the first phase. This resulted in smooth material flow without hesitation effect and filling was better compared to the existing design (Fig. 1). The process was optimized to achieve the best cycle time with reduced cost and operated at low pressure. These were done by performing various runs and then compare the graph to finalize the best solution. Simultaneously, the temperature, pressure and thermal residual stresses around the electronic component were also controlled.
Fig. 1 We can observe the flow is not uniform in the original design (left) and there is flow hesitation in some areas like connector area. In new proposal (right) with 2 gates, we can observe the flow is uniform
and the flow hesitation has almost been eliminated.
The simulation was generated for the existing design with the help of Moldex3D. All the observation was noted and the action plan was created with respect to process changes and design changes. The results obtained from simulation for the existing design were close to the real scenario. This was verified with the process data sheet from the production. The identified defects in the existing design were also observed in the existing product as shown in Fig. 2. After the design changes, Moldex3D was used to simulate both the original design and the optimized design. The design was optimized taking into account all the identified problems from the existing design. Additionally, the cycle time was optimized to reduce production time and cost. When compared with the actual mold trial results, SKF’s technical centre found that Moldex3D simulation analysis results had strong correlation with the real scenario.
Fig. 2 High correlation between simulated and actual manufactured part is shown. A sink mark is identified on the simulated model (left) and the same result is visible in the prototyped part (right).
Results
Through Moldex3D analysis, SKF could clearly understand the filling behavior and predict probable defects due to process parameters and design deviations prior to prototyping and production. This saved a large, valuable amount of product development cycle time due to early investigation using Moldex3D tool. The accuracy of Moldex3D simulation analysis was verified with the actual manufacturing process sheet and visual inspection. The result helped their technical centre to optimize the process parameters, identify and fix defects in product and also correlate the cause of product failures at end application with the identified defects.
Tuk tuk motorcycles, Electric tuk tuk, Electric tuk tuk price, Tuk tuk motor electric
Xuzhou Hezhan Locomotive Co., Ltd , https://www.hezhanvehicle.com