1, large work table, to adapt to a large area of ​​sheet metal stamping and automatic progressive die production, high work efficiency.
1. Extra large worktable, suitable for great area sheet metal pressing and automatic step molding production, high working efficiency.
2, high-quality steel plate welding body, improve the machine strength and stiffness.
Steel welded body enhancing the intensity and rigidity of the machine.
3. The large gears and gear shafts are ground precisely. The machine tool has low noise and stable operation.
Precisely grinded rack wheel and wheel shaft, low machine operation noise and stable operation.
4, using dry or wet pneumatic friction clutch - brake, sensitive action.
Adoption of dry or wet pneumatic frictional clutch-detent, the movements are sensitive.
5. Double crankshaft reversing transmission has good synchronization and strong anti-unloading ability.
Adoption of dual-crooked shaft converse transmission, providing excellent synchronization and strong anti carry-deflection capability.
6. The slider adopts six-sided rectangular guide rails with good guide and high precision.
Slide blocks with six-sided rectangle gui derail, the guidance is excellent and the precisions are pinpointed.
7, stepless adjustment of the motor device, to adapt to different stamping process requirements.
Stepless gearings motor or device, fitting the craftsmanship of different pressing parts.
Standard accessories1, hydraulic overload protection device. | Hydraulic over loading protection system. |
2, automatic lubrication device. | Automatic lubricating system. |
3, mold height electric adjustment device. | Mould installation height adjustment device. |
4, stepless speed motor device. | Stepless gearing electromotor device. |
5, digital display high indicator. | Digital display mould height indicator. |
6, slider and die balance device. | Balance unit for slide block and mould. |
7, electronic cam control system and mobile cabinet. | Electronic cam controller system and movable electrical equipments control box. |
8, removable two-hand operation box | Movable operation box for both hands. |
9, air blowing device. | Air power material blowing device. |
10. Shockproof rubber pads. | Shock resist rubber mat. |
1, airbag mold pad device. | Air bag mould mat device. |
2, photoelectric safety device. | Photo electricity safety device. |
3, foot switch. | Pedal power switch. |
4, automatic feed output shaft. | Automation on feeding output shaft. |
5, automatic feeder. | Automatic feeding device. |
6, rapid mold change device. | Papid mold displacing unit. |
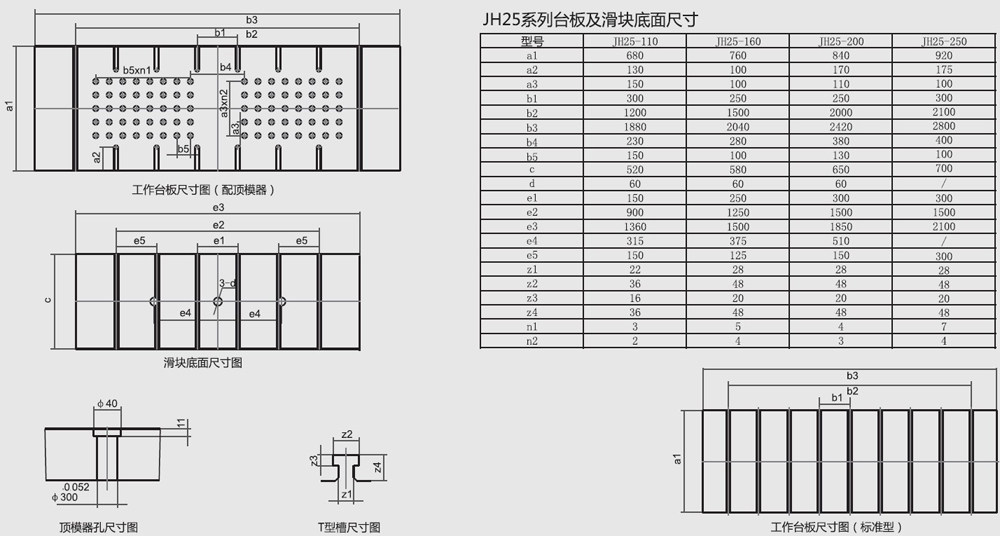
Click on the picture to see a larger image
Model/Technical Parameter Model/Technical parameters | JH25-110 | JH25-160 | JH25-200 | JH25-250 | JH25-315 | ||||||||
L | S | L | S | L | S | L | S | L | S | ||||
Slider nominal pressure (KN) Slider nominal pressure (KN) | 1100 | 1600 | 2000 | 2500 | 3150 | ||||||||
Capacity position (mm) Capacity engender position (mm) | 5/3 | 6/3.5 | 7/4 | 7/4 | 7/4 | ||||||||
Slider stroke (mm) Slide block stroke (mm) | 180/110 | 200/130 | 250/150 | 250/150 | 280/180 | ||||||||
Stroke frequency (SPM) | L | 35-65 | 30-55 | 25-45 | 25-40 | 20-35 | |||||||
S | 45-80 | 40-75 | 35-60 | 30-55 | 30-50 | ||||||||
Closed height (mm) Max closing height(mm) | 400/435 | 450/485 | 500/550 | 550/600 | 550/600 | ||||||||
Closed height adjustment (mm) Closing height adjust measurement(mm) | 90 | 100 | 110 | 120 | 120 | ||||||||
Slider center distance from body (mm) Distance between the center of the slide block and the body(mm) | 350 | 390 | 430 | 450 | 450 | ||||||||
Worktable to ground distance (mm) Distance between the worktable and ground (mm) | 900 | 900 | 1,000 | 14100 | 1100 | ||||||||
Table size (mm) Worktable measurements (mm) | Left Right | 1880 | 2040 | 2420 | 2700 | 2700 | |||||||
Before and after Front Behind | 680 | 760 | 840 | 920 | 920 | ||||||||
Slider bottom plane size (mm) Plane dimension of the slide block bottom (mm) | Left Right | 1360 | 1500 | 1850 | 2100 | 2100 | |||||||
Before and after Front Behind | 520 | 580 | 650 | 700 | 700 | ||||||||
Dimensions (mm) Outline (mm) | Left Right | 2170 | 2340 | 2720 | 2970 | 2990 | |||||||
Before and after Front Behind | 1790 | 2040 | 2500 | 2750 | 2950 | ||||||||
High Height | 3130 | 3823 | 4050 | 4350 | 4360 | ||||||||
Airbag Airbag | KN Propping capacity KN | 35×2 | 63×2 | 80×2 | 100×2 | 140×2 | |||||||
Stroke mm Stroke mm | 70 | 80 | 90 | 100 | 100 | ||||||||
Roof area mm Propping plate acreage mm | 350×220×2 group | 410×220×2 group | 460×340×2 groups | 540×420×2 group | 560×420×2 group | ||||||||
Motor Power (kw) Electromotor Power (kw) (Fixation/Variable) | 15 | 18.5 | twenty two | 30 | 37 | ||||||||
Weight (kg) Weight (kg) | 14500 | 21000 | 28500 | 38000 | 42500 | ||||||||
Use air pressure (Mpa) Air pressure used (Mpa) | 0.5 | 0.5 | 0.5 | 0.5 | 0.5 |
Technical specifications are subject to change without notice!
Hydroxypropyl Cellulose,Industrial Grade Adhesives,Hydroxypropyl Cellulose Degradation,Industrial Grade Hydroxypropyl Cellulose
Henan Kepeiao New Materials Co.,Ltd. , https://www.kopeochem.com