Introduction: Graphite is a very easy to cut material, but because the graphite material used as EDM electrode must have sufficient strength to avoid damage during operation and EDM processing, at the same time the electrode shape (thin-walled, small rounded, sharp change ), etc. also put forward higher requirements on the grain size and strength of the graphite electrode, which results in the graphite workpiece is easily disintegrated during the processing, and the tool is easy to wear. The high cost, low efficiency, and often scrapped workpieces are the cause of the processing of the company. How to better process graphite electrodes?
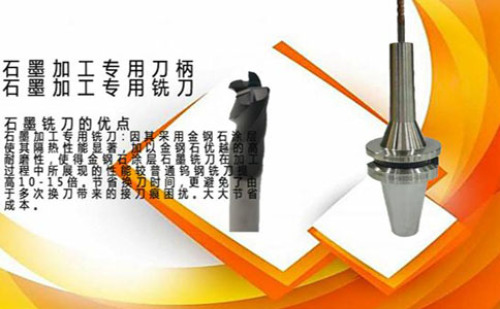
A: Several issues affecting tool wear
1. For the processing of graphite special tools, the ordinary TiAlN coating can be selected appropriately on the material selection of a relatively good tool material, that is, a little higher cobalt content; for diamond-coated graphite tool, can be selected on the material The appropriate choice of a relatively good hardness, that is, a little lower cobalt content;
2, the geometry of the tool: graphite tool to select the appropriate geometric angle, help reduce the tool vibration, in turn, graphite workpiece is not easy to collapse; 1 front corner, when the negative front angle processing of graphite, the tool edge Good strength, good resistance to impact and friction, with the decrease of the absolute value of the negative rake angle, the wear area of ​​the flank surface does not change much, but it tends to decrease overall. When using the positive rake angle machining, with the rake angle The increase in the tool edge strength is weakened, but will lead to increased flank wear. When the negative rake angle is processed, the cutting resistance is large and the cutting vibration is increased. When the rake angle is used for machining, the tool wear is severe and the cutting vibration is also large. 2 In the rear corner, if the relief angle increases, the tool edge strength decreases and the flank wear area gradually increases. After the tool clearance angle is too large, the cutting vibration increases. (3) When the helix angle is small, when the helix angle is small, the longest blade length of the same workpiece is cut into the graphite workpiece at the same time, the cutting resistance is maximum, and the cutter is subjected to the largest impact force. Therefore, the tool wear, the milling force and the cutting vibration are the largest. When the helix angle is larger, the direction of the resultant force of the milling deviates from the surface of the workpiece, and the cutting impact caused by the disintegration of the graphite material is intensified, so that the tool wear, the milling force and the cutting vibration also increase. Therefore, the effect of tool angle change on tool wear, milling force, and cutting vibration is a combination of rake angle, relief angle, and helix angle. Therefore, attention must be paid to the selection. Through a large number of scientific tests on the processing characteristics of graphite materials, PARA cutters optimize the geometric angle of the relevant tools, thereby greatly improving the overall cutting performance of the tool.
3, the tool coating: processing of graphite tools should choose diamond coating, its high hardness, good wear resistance, low friction coefficient, etc., at this stage diamond coating is the best choice for graphite processing tools, but also the most able to reflect The superior performance of the graphite tool; The advantage of the diamond coated carbide tool is that it combines the hardness of the natural diamond and the strength and fracture toughness of the cemented carbide; it can improve the tool life of nearly 10-20 times.
4. Reinforcement of tool edges: The tool edge passivation technology is a problem that has not been widely considered by people and is an important issue. There are microscopic gaps (ie, micro-disintegration and sawing) with different degrees of extent in the edge of the hard alloy tool after diamond grinding. High-speed cutting tool performance and stability of graphite put forward higher requirements, in particular, diamond-coated tools in the coating before the knife must pass through the passivation treatment in order to ensure the coating's solidity and service life.
5, the tool machining conditions: Select the appropriate processing conditions for the life of the tool has a considerable impact. 1 Cutting method: Down milling. 2 Insufflation (or vacuuming) and impregnating EDM fluid processing to remove the graphite dust on the surface of the workpiece in time will reduce the secondary wear of the tool and prolong the service life of the tool. 3 Select the appropriate high speed and the corresponding large feed. To summarize the above points, the material, geometric angle, coating, cutting edge strengthening, and machining conditions of the cutters play different roles in the service life of the cutter. They are indispensable and complementary. A good graphite tool should have a smooth graphite powder flutes, a long service life, be able to deepen the engraving process, and save processing costs.
The advantages of graphite milling cutters
Special milling cutter for graphite processing: Due to its diamond coating, its thermal insulation performance is remarkable, and the superior high wear resistance of diamond makes the performance of diamond coated graphite cutter exhibited during processing. It is 10-15 times higher than ordinary tungsten steel cutters. Save tool change time and avoid troubles caused by multiple tool change. Significant cost savings.
Efficiency: The Automatic food Packing machine Integrate Bag-making, filling, sealing, cutting, heating, date / lot number achieved in one progress
Intelligent: Packing speed and bag length can be set on the Touch screen without changing any parts of the machine
Durability:Independent temperature controller with heat balance enables different packing materials; Dual inverters controller, upgradable PLC system, self-failure diagnosis, double encoder.
Automation: Automatic stop function, with safe operation and saving the film. One worker is able to operate it , Saving labor costs.
Convenient: Easy to operation and maintenance.The machine can be moved to any workplace, whether it is a home or a factory.
Versatility: One packing machine is able to pack various kinds products, like food, medicine, daily appliances,cosmetic,metals, industrial parts, boxes, trays, toys. It also can connect with other production line working .
Customizable:The length of the machine can be appropriately shortened according to customer requirements. The machine can also be converted to dual servo control by variable frequency control.
Flow Wrapping Machine,Flow Pack Machine,Flow Wrap Packing Machine,Flow Wrapper Packaging Machine
Ruian Science Machinery And Technology Co., Ltd. , https://www.science-pack.com