An automatic lubrication system (ALS), often referred to as a centralized lubrication system, is a system that delivers controlled amounts of lubricant to multiple locations on a machine while the machine is operating. Even though these systems are usually fully automated, a system that requires a manual pump or button activation is still identified as a centralized lubrication system. The system can be classified into two different categories that can share a lot of the same components.
 Oil systems: Oil systems primary use is for stationary manufacturing equipment such as CNC milling
 Grease systems: Grease primary use is on mobile units such as trucks, mining or construction equipment.
 A typical system consists of controller/timer, pump w/reservoir, supply line, distributors/metering valves, and feed lines.
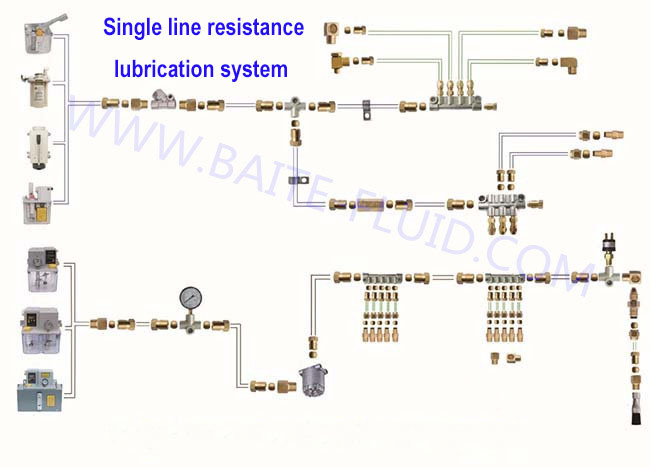
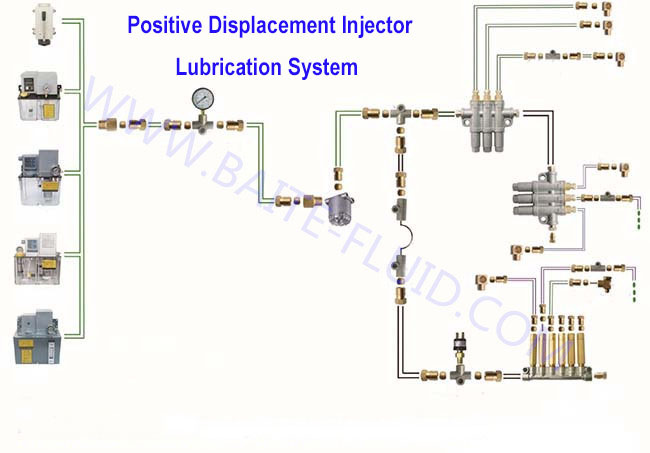
Production instructions
 Our products are complete, including various lubrication pumps( such as manual and electric pumps), minimal quantity lubrication units, lubricant distributors( such as pre-lubrication distributors, re-lubrication distributors, progressive feeders, metering units), filters, other accessories( such as brushes, nozzles and spray heads, reservoirs), various connectors, tubes. Widely use in CNC machinery, machining center. We can provide you with the most suitable lubrication system design, products and services according to your requirements. With years of experience and the ability to continuously develop new technologies, we create products that offer competitive advantages to our customers.
Main Product
Oil Lubrication System | Manual Type Oil Lubricator |
Intermittent Type Oil Electric Lubricator | |
Oil Electric Lubricator - With Control by PLC | |
Oil Electric Lubricator - With Control by TIMER | |
Grease Lubrication System | Manual Type Grease Lubricator |
Grease Pneumatic Lubricator | |
Grease Electric Lubricator - With Control by TIMER | |
Grease Electric Lubricator - With Control by PLC | |
Circulating Type Oil Lubrication System | Circulating Oil Electric Lubricator |
Oil Filler Pneumatic Pumps | |
Motor - Rotary Oil Pump | |
Circulating Coolant Pump | |
Distributor & Accessories | Various Kinds of Distributor |
Hose Spray gun | |
Fitting Parts Brass | |
Pipes - Flexible Hose |
Product Show
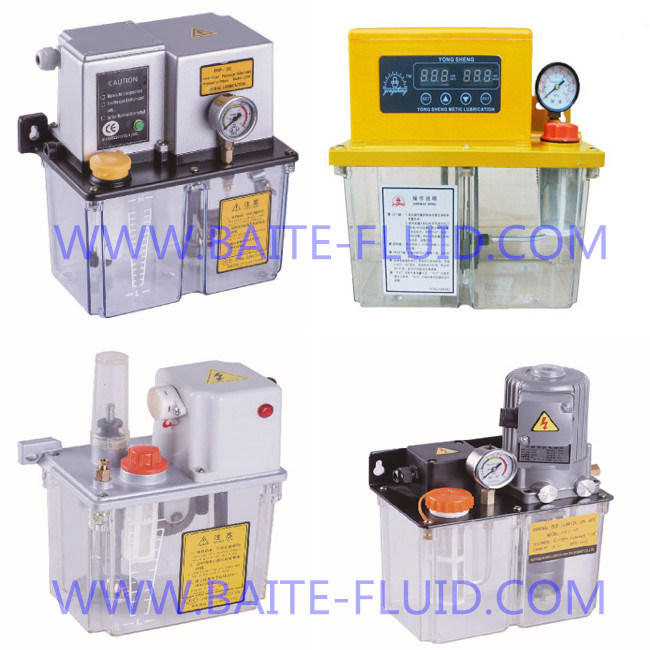
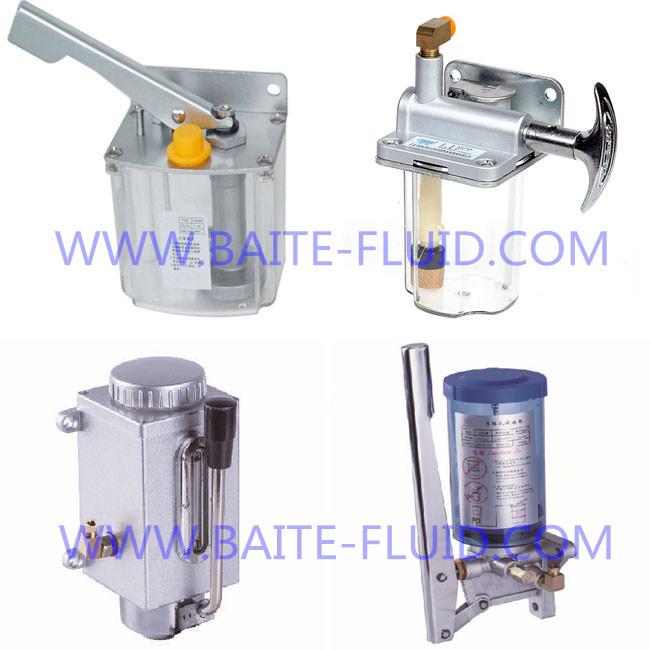
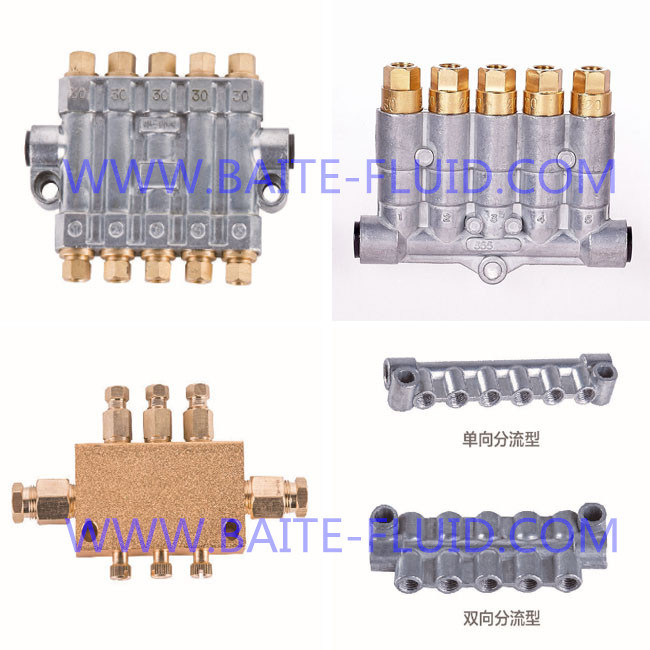
Quality Assurance
Raw material inspection(5steps)- Raw materials testing is to ensure the raw material conforming to the order requirements.
Process testing(10steps)-Each processing step testing is to guarantee each step product qualified.
Factory testing(6steps)-Assure 100% product qualified rate to meet customer's requirements
Contact Us
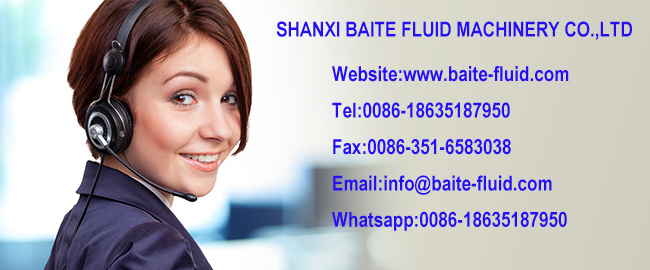
Â
 An automatic lubrication system (ALS), often referred to as a centralized lubrication system, is a system that delivers controlled amounts of lubricant to multiple locations on a machine while the machine is operating. Even though these systems are usually fully automated, a system that requires a manual pump or button activation is still identified as a centralized lubrication system. The system can be classified into two different categories that can share a lot of the same components.
 Oil systems: Oil systems primary use is for stationary manufacturing equipment such as CNC milling
 Grease systems: Grease primary use is on mobile units such as trucks, mining or construction equipment.
 A typical system consists of controller/timer, pump w/reservoir, supply line, distributors/metering valves, and feed lines.
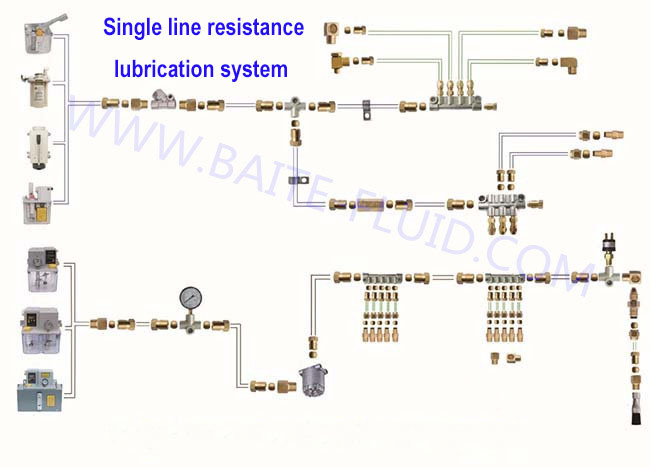
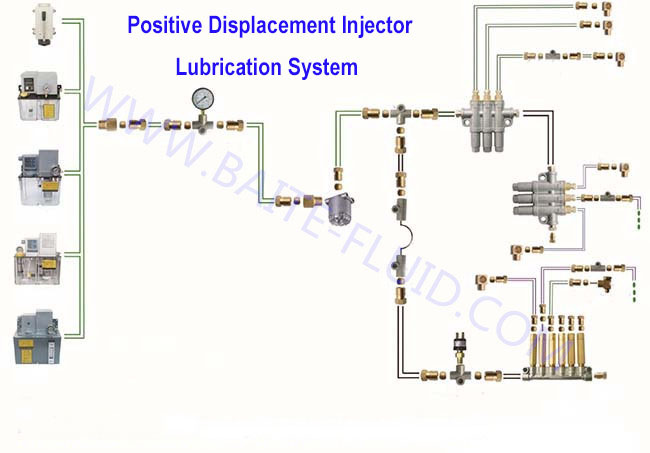
Production instructions
 Our products are complete, including various lubrication pumps( such as manual and electric pumps), minimal quantity lubrication units, lubricant distributors( such as pre-lubrication distributors, re-lubrication distributors, progressive feeders, metering units), filters, other accessories( such as brushes, nozzles and spray heads, reservoirs), various connectors, tubes. Widely use in CNC machinery, machining center. We can provide you with the most suitable lubrication system design, products and services according to your requirements. With years of experience and the ability to continuously develop new technologies, we create products that offer competitive advantages to our customers.
Main Product
Oil Lubrication System | Manual Type Oil Lubricator |
Intermittent Type Oil Electric Lubricator | |
Oil Electric Lubricator - With Control by PLC | |
Oil Electric Lubricator - With Control by TIMER | |
Grease Lubrication System | Manual Type Grease Lubricator |
Grease Pneumatic Lubricator | |
Grease Electric Lubricator - With Control by TIMER | |
Grease Electric Lubricator - With Control by PLC | |
Circulating Type Oil Lubrication System | Circulating Oil Electric Lubricator |
Oil Filler Pneumatic Pumps | |
Motor - Rotary Oil Pump | |
Circulating Coolant Pump | |
Distributor & Accessories | Various Kinds of Distributor |
Hose Spray gun | |
Fitting Parts Brass | |
Pipes - Flexible Hose |
Product Show
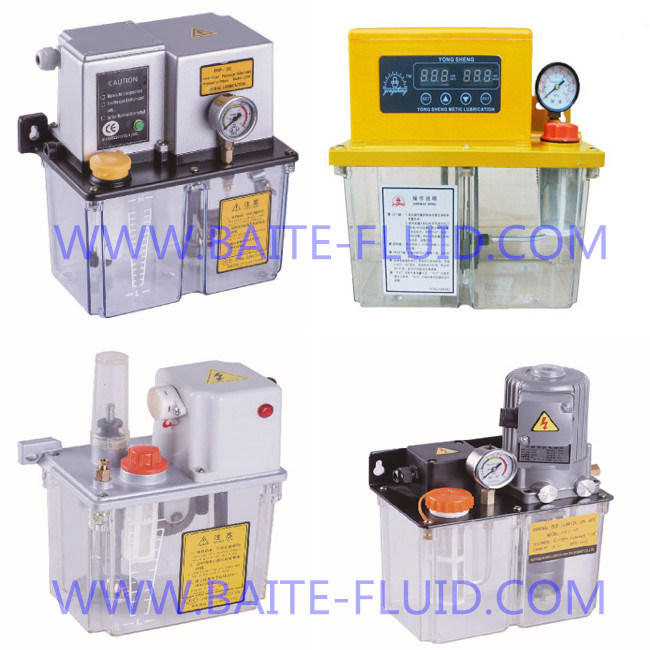
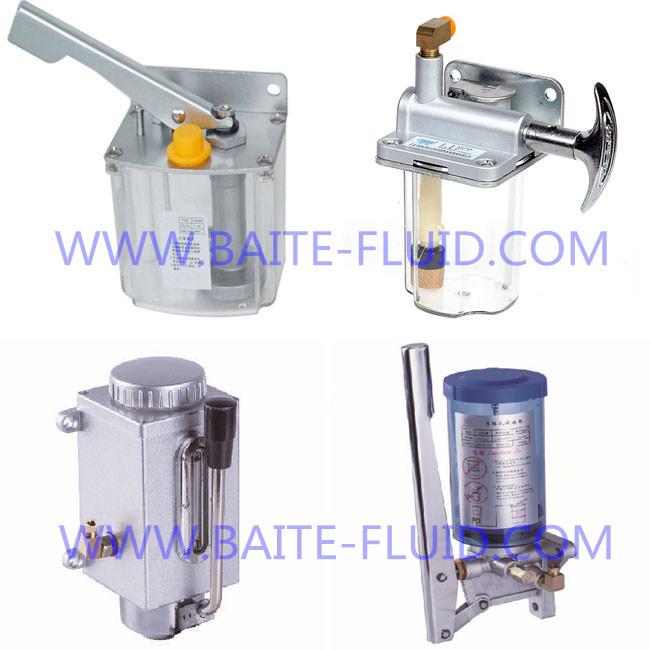
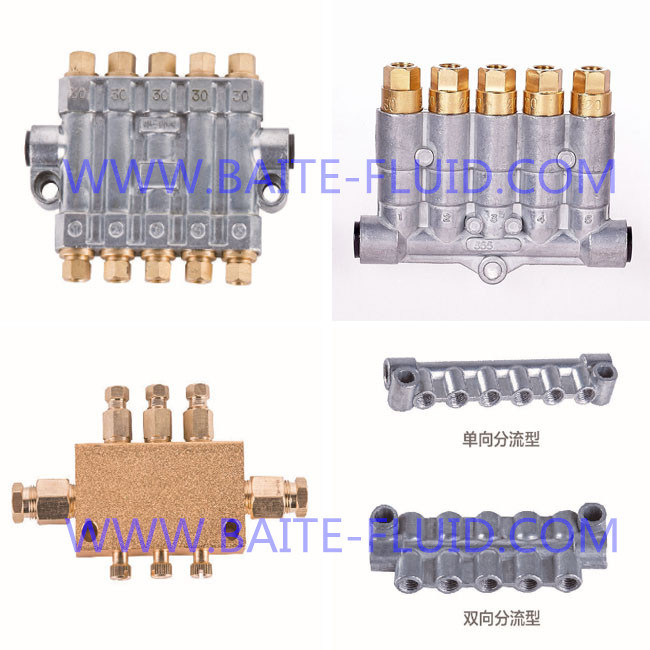
Quality Assurance
Raw material inspection(5steps)- Raw materials testing is to ensure the raw material conforming to the order requirements.
Process testing(10steps)-Each processing step testing is to guarantee each step product qualified.
Factory testing(6steps)-Assure 100% product qualified rate to meet customer's requirements
Contact Us
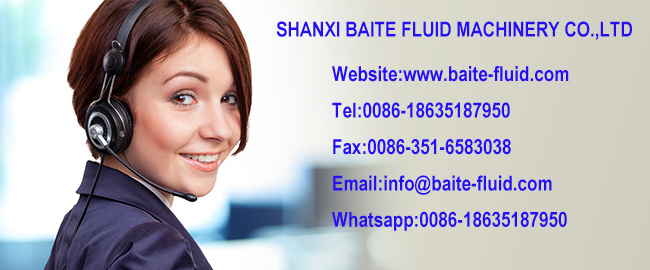
Â
Starch Filter Press are used highly successfully to dewater the starch in the conical centrifuges employed in this sector. The drum filters used in starch filtration applications are fitted with our filtration meshes. We offer matching filter meshes and complete sieving screens in the air separators which used in the field of solid-solid separation.
Working Principle
Membrane Filter Press Plates have a chamber below the drainage surface that can be inflated. The common method used is water pressure, which is generated by pumping into the squeeze cavity to inflate the face of the plate against the filter cake. Membrane Plates are used to reduce the cake moisture content & shorten the filtration cycle time.
During the initial phase of the filtration cycle, so-called [fill and filtration" the process is similar to the Chamber Filter Press. After reaching a predefined pressure, usually around 5 - 7 bar, depending on the sludge characteristics, sludge feeding is stopped & the rubber membranes inflated, using either water or air as squeeze medium. The cake is hereby compressed and dewatered further. Then the squeeze medium is relieved & the cake discharged.
Features of Food-Grade Filters
(1) |
Patented Filter Plate design minimizes product retention and prevents contamination |
(2) |
Sanitary valves and pipe fittings |
(3) |
Clean-In-Place System - automatically cleans the filter and piping to eliminate cross contamination |
(4) |
Structure Cladding - equipment stays clean |
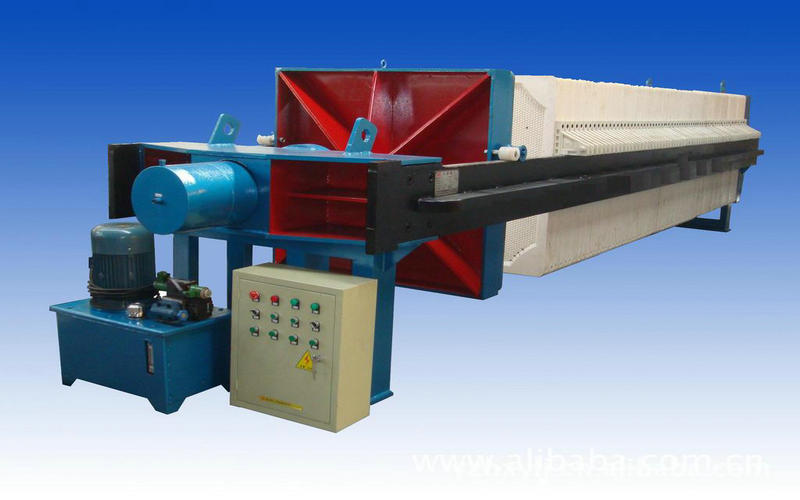
Starch Filter Press
Food Beverage Filter Press, Automatic Hydraulic Membrane Filter Press,Filter Press For Starch Industry
Hebei TianGuan Filter Press Co., Ltd. , http://www.filterpressure.com