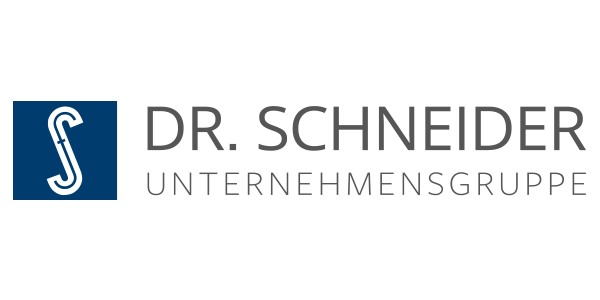
- Customer: Dr. Schneider
- Country: Poland
- Industry: Automotive
- Solution: Moldex3D Advanced; Flow, Pack, Cool, Warp, MCM, Digimat-RP, Fiber, FEA Interface, Expert, Advanced Hot Runner, Viscoelasticity,Â
CADdoctor - View PDF Version
Executive Summary
Przemyslaw Narowski, CAE Engineer at Dr. Schneider explains how the true need for an injection molding simulation process emerged within his company and why Moldex3D was chosen. Moldex3D is used in a feasibility study of a newly designed part, and the extended use of Moldex3D’s other simulation solutions broaden their technical capabilities and the future outlook for a streamlined engineering workflow from CAD, through CAE to CAM. Multiple real cases are shown in his story to illustrate the accuracy of Moldex3D’s results and the values.
Challenges
- Surface defects caused by air traps
- Serious product warpage
- Find effective venting of the cavity
Solutions
In the case of a fuel filler part, Moldex3D is used to reduce the warpage amount by 40% to ensure dimensional accuracy. Moldex3D also helped eliminate air traps on the surface of an automotive interior part.
Benefits
- Test new designs for part feasibility such as the ideal gate locations and the estimated cycle time
- Solved difficult molding challenges, such as warpage (by 40%) and air traps
- Inspire “Reverse Simulation†concept for the future product development direction
Case Study
The main objective is to validate the accuracy of Moldex3D simulation results comparing with real experimental case and further prevent the high warpage and visible air trap issue on the product.
In the first case, Dr. Schneider utilized Moldex3D to simulate the warpage behavior of a guiding element (Fig. 1) and the lever of a car phone box (Fig. 2), and found the simulation results match the experiment results.
* The match between simulation and real warpage is near perfect
Fig. 1 The warpage results of simulation and reality of the guiding element
Fig. 2 The warpage analysis result vs. real measurement
In the second case, excessive warpage and air traps were predicted in the fuel filler lever and its lid by using Moldex3D. These potential problems might result in failure in assembling and affect the cosmetic appearance of the part.
With the help of Moldex3D, Dr. Schneider developed a new design, which minimized the amount of material in the area of the highest shrinkage by half (Fig. 3) and identified suitable venting locations (Fig. 4). As a result, the prediction showed that the total warpage displacement was significantly improved.
Fig. 3 The optimized design minimized the amount of material by half in the area of the highest shrinkage
Fig. 4 Moldex3D can precisely predict the locations of air traps and identify suitable venting locations.
Dr. Schneider used Moldex3D to simulate the original design and the optimized design. The analysis result of the original design showed that high shrinkage would occur in the thick areas of the part (Fig. 5) and result in excessive warpage. After changing the part thickness, the prediction showed that the warpage displacement has been reduced by almost 40% (Fig. 6).
Fig. 5 Excessive warpage was predicted in the original design
Fig. 6 Â total warpage displacement has been reduced by almost 40%
Results
Through Moldex3D analysis, Dr. Schneider clearly understood the filling and warpage behavior and was able to predict potential defects prior to actual production. Nowadays at Dr. Schneider, Moldex3D is one of the most important tools used in feasibility studies in the product development stage. Every injection molded design must go through mold filling analysis. If something goes wrong, for example, when warpage values are inacceptable, Dr. Schneider’s team will take corrective action. In the end, Dr. Schneider is able to successfully solve manufacturing issues and optimize product and mold designs, which helps them efficiently reduce mold trials and mold modification costs before actual production.
Â
Alcohol Pad Packaging Machine,Alcohol Pad Packaging Machine for Medical Use,Medical Alcohol Tablet Making Machine
Changzhou shanglai automation equipment co., ltd , https://www.slautomate.com