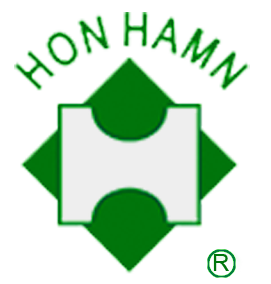
Founded in 1987 , Hon Hamn Enterprise Co., Ltd. stands at San Chung Dist, New Taipei City, Taiwan, specializing in foam materials for air conditioning, computer, office appliance and packaging industries. In 2004, three factories were set in Dongguan City, China, which are Plastic injection molding plant, Mold tooling plant and Foam processing plant.
The company started to stride over exporting foam materials to air-conditioner factories in the middle east and later to America, Canada, Singapore, Thailand, the Philippines, and Australia…etc; products ranging from hardware, copper pipe, valves, screws, sheet metal dies, plastic injection molds, plastic injected products and various types of machinery. Hon Hamn has implemented Moldex3D to conduct early product reviews during product development and design stages.
Â
Challenges
Split air conditioners have started to grow in popularity in recent years. The design of air conditioner panels tends to be thin and light in order to meet stylish and lightweight requirements. Large parts like air conditioner external shells usually rely on multi-cavity injection molding method, which has little control over flow fluidity and product deformation, easily resulting in warpage problems.
Solutions
- Multi-gates Location Optimization: Evaluate the flow results of different runner systems and gate configurations for achieving the optimal design.
- Uniform and Lower Shrinkage Control: Moldex3D is able to provide high precision simulation analysis capability which can successfully validate better runner designs with uniform and lower shrinkage.
Values
Moldex3D plastic injection molding simulation software has been adopted by Hon Hamn Corporation as the standard tool for design verification and optimization. The high accuracy of simulation results also makes Moldex3D the most useful tool to convince customers to optimize mold designs. Moldex3D not only can reduce mold trial iterations and the risk of opening molds. Moreover, Moldex3D can help establish design model database for each mold/ product and further generate new customers, enhancing OEM capabilities.
Case Study
During the simulation process, many issues can be further discussed based on different needs and viewpoints. From the viewpoint of mold manufactures, the key point of precise analysis is the key to solve customer’s problems due to the limited time-to-market.
The following is a optimization case study of a split air conditioner shell from Hon Hamn Corporation. Through the accurate in-depth simulation analysis, the company is able to validate plastic parts and make design iterations based on client’s demands then choose the best design from the simulation results.
Various Runner and Gate Configurations Evaluation
Moldex3D presented flow balance solution, especially targeting at large and flat products in this case. Moldex3D, the true 3D injection molding simulation software, is able to provide accurate comparison of simulation results based on various design iterations (Fig. 1). Figure 2 shows the comparison result of 90% melt front time and we can see Design 4 has better flow performance. Based on the analysis result of flow balance, we can choose designs with better flow balance to conduct warpage comparison. The ultimate goal is to achieve an optimal design with uniform and lower shrinkage on both sides of the air conditioner shell.
We can learn from the six sensor nodes warpage comparison chart (Fig. 4) that Design 4 and Design 5 have uniform shrinkage, which is easier for warpage trend prediction and field control. In addition, it is also known that Design 4 and 5 can optimize and lower warpage problems, greatly enhancing the manufacture quality of the mold assembly.
Fig. 1 Â The original runner and gate designs vs the proposed designs
Fig. 2 Â Compare melt front time result at 90% between six designs
Fig. 3 Â Compare Z-displacement predictions
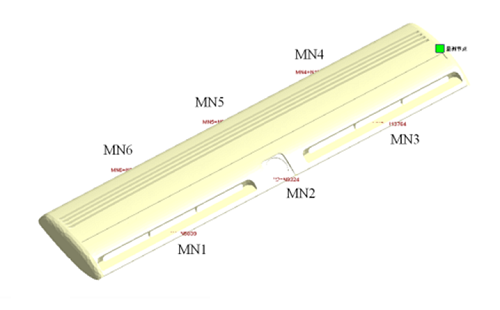
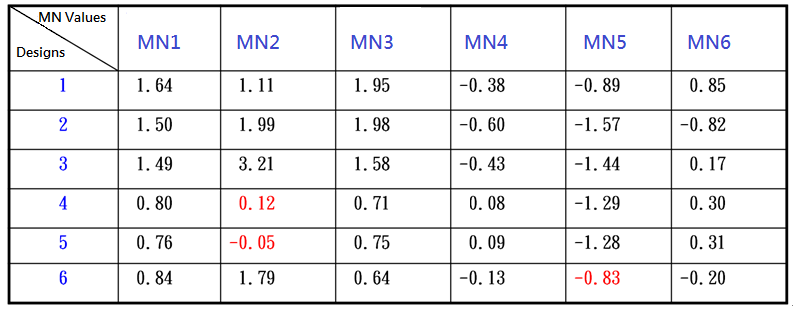
Fig. 4 Â Compare six sensor nodes warpage values
Fig. 5 Â Compare Z-displacement values and directions between six designsÂ
Moldex3D enables OEMs to extend their business to more customers
Moldex3D not only can help customers solve design defects, shorten time-to-market and minimize the risk of  rework and redesign. Moldex3D can further assist customers to build design model database for each product/mold, which helps customers accumulate design knowledge and obtain a solid grasp of the product know-how and know-why. With help from Moldex3D plastic injection molding software, OEM manufacturers can ensure competitiveness and profitability and also ramp up their ODM capability.
Bicycle Seats For Men,Mountain Bike Seat With Spring,Road Bike Saddle With Spring
Xingtai Yiming Bicycle Co., Ltd , https://www.ymbicycleparts.com