Foreword The pursuit of excellence in every detail is the pursuit of excellent companies. It is also why we see the increasingly elegant packaging of Budweiser and Tsingtao in supermarkets. This is a key part of attracting consumers, except for the quality of beer. The exquisite packaging also embodies the producers' grasp and pursuit of detail quality, which also brings new opportunities for printing presses.
In addition, the requirements for environmental protection in the beer and beverage industry are also more stringent. In order to reduce the harm to the human body in the production process, environmental protection printing is also paid more attention, which also makes flexographic printing gradually reflected its advantages over offset printing and gravure printing. .
1. System Requirements Width Flexo Printing Due to its high requirements on the precision of machined parts, wide-format flexo printing has not been vigorously developed for a long period of time. At present, this model is mainly used for The printing of corrugated paper is known as the “preprinting technique†using this printing process. In contrast, the printing after the production of corrugated cardboard is called the “postprinting technologyâ€. Compared with the postprinting technology, the printing is preprinted. Technology has its unique advantages:
Preprinting technology is efficient and of good quality. For the printing of corrugated board, the preprinting technology is to link the printed good paper with the corrugated line, and the cartons can be directly produced without the need to transfer to the slot printing machine like the post-printing technology. , And, it is different from the post-printing technology, it will not cause pressure on the corrugated paper, thereby affecting the strength of the corrugated box.
Environmental protection. Flexographic printing uses water-based inks, which are more environmentally friendly than oil-based inks, and have a smaller impact on the air and on the production floor.
Larger format. For a wide flexo, a 1200 mm to 2200 mm printed web can provide surface printing of large packaging containers, and can also provide printing of multiple products simultaneously by slitting.
The system required to achieve a printing speed of 300m/min, printing accuracy +/-0.1mm, width 1200mm.
2. Equipment composition and working principle The unit consists of unwinding, front traction unit, rear traction unit, printing color group (generally no more than 9 colors), and rewinding unit, as shown in Figure 1.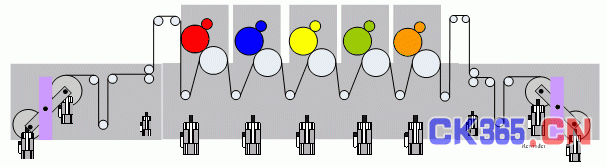
2.1 Unwinding unit The unwinding section is mainly composed of an air brake and a tension swing roller. The material winding core is placed on the unwinding rack through the air expansion shaft. When the air brake brake air pressure is zero, the material roll and the air expansion shaft are together. Can be free to rotate; In normal work, by adjusting the air pressure (proportional valve: 0 ~ 10VDC represents the pressure from small to large) to adjust the braking force and control the unwinding tension, the specific working principle shown in Figure 2.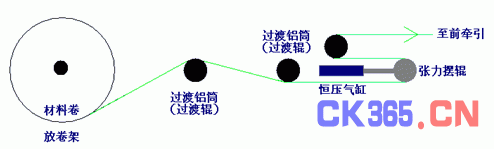
The tension roller keeps a constant thrust (the pressure in the cylinder is constant). In normal operation, we adjust the air pressure of the air brake through the PID so that the tension roller stays in the set position (the position of the tension roller is installed in the pendulum. The potentiometer on the roll detects it, 0~10V means, generally adjust the middle value to 5V), this maintains the constant tension of unwinding, which is also the first level of tension control before the material enters the printing.
2.2 Front traction part The front traction part is composed of front traction motor, front traction roller, front traction roller and a tension swing roller. The role of the front traction part is to send the printing material to the printing part with a constant tension. The working principle is shown in Figure 3.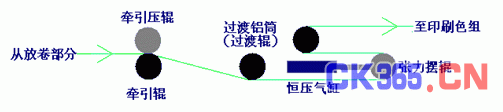
The traction roller is driven by a traction motor, and the traction roller presses on the traction roller during normal operation to prevent the material from slipping. In normal operation, the PID adjusts the speed of the front traction motor to control the tension swing roller at the set position, thereby maintaining a constant material tension. This is the second level of tension control before the material enters the printing section. At the same time, the front pulling pressure roller also acts as a tension isolation, and the tension fluctuation of the unwinding portion can be isolated.
2.3 printing part of the printing part by the color group, 7 color is a 7 color group; each color group consists of color group motor, bottom roller, plate roller, ink roller composition. The color group motor drives the bottom roller through a gear box, and the plate roller, the bottom roller and the ink feeding roller are put together by gears. The principle of work is shown in Figure 4.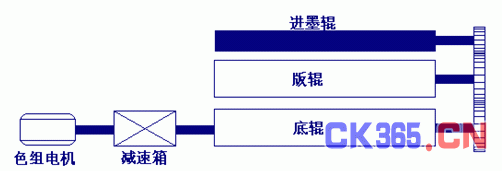
Plate rollers, bottom rollers, and ink inlet rollers are matched by gears to ensure consistent surface line speed; before starting printing, there is a gap between the plate roller and the bottom roller, and the plate roller is in the raised state. The surface and the printed material are not in contact. When the plate roller is lowered, the surface of the plate roller is kept in light contact with the surface of the substrate to be printed, and the contact pressure between the plate surface and the material can be adjusted according to the printed pattern effect. The down roller is the plate roller and the ink feed roller. The order of the plate roller is: Stop the ink roller for 2 seconds, then back off the plate roller, keep the plate roller back signal and the ink roller stop signal for 2 seconds. Then both signals are reset. In normal printing, all color groups printed are kept in strict position synchronization, and all color group calibrations are exactly the same. Between the color group and the color group, the heated portion of each color group is printed and heated by hot air; the hot air is sent out by the total blower; each color group has a heater, which is divided into fast heating and slow heating. There are two types of heating: heating wire and steam.
2.4 Rear traction part The rear traction part is composed of a rear traction motor, a rear traction roller, a rear traction roller and a tension swing roller; the function of the rear traction part is to bring the printing material out of the printing part with a constant tension. The working principle diagram is shown in Figure 5.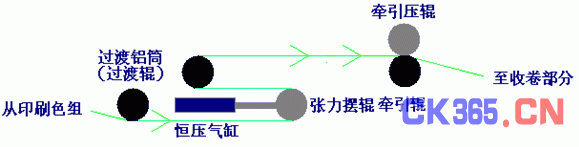
The tension roller is installed between the last color group and the rear traction. Just like the front traction, during normal operation, the traction roller is also pressed on the traction roller to prevent the material from sliding, and at the same time, it plays the role of tension isolation; the system is based on the oscillating roller. The setting position of the traction motor is regulated by the speed of the PID to stabilize the swing roller at the set position so as to stabilize the rear traction tension.
2.5 The winding part of the flexographic printing press adopts the surface friction winding method. The winding part is mainly composed of a tension swing roller, a friction roller, and a passive air expansion shaft. Its working principle diagram is shown as in Fig. 6.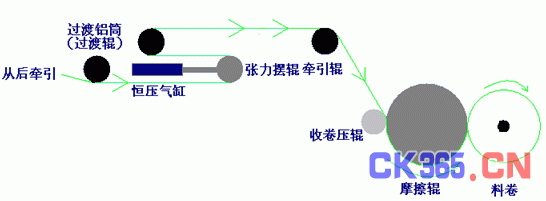
The friction roller is driven by a third-party asynchronous motor. The motor is driven by ACOPOS or vector inverter. During normal operation, the take-up roller presses the material on the friction roller surface, and the take-up roller also presses on the friction roller surface; the system passes tension. Comparison of the setting position and actual position of the pendulum roller The speed of the friction roller drive motor is adjusted by the PID, and the tension roller is controlled to stabilize at the set position to achieve constant tension winding. The friction roller and the pressure roller are soft rubber rollers.
3. Control System Hardware Configuration The hardware configuration of the system is shown in Figure 7. It is mainly composed of a PowerPanel - man-machine interface with integrated control, display and operation, multiple ACOPOS intelligent servo drives and EthernetPOWERLINK real-time communication Ethernet. constitute.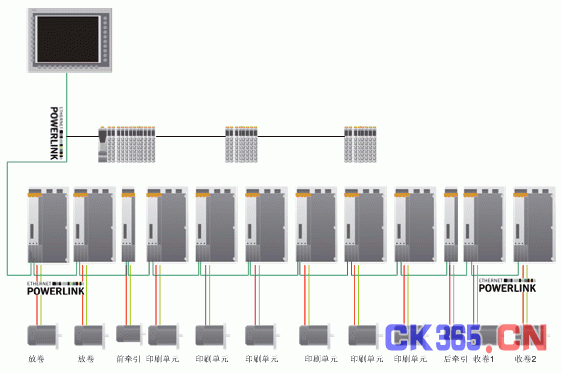
4. Key technologies and solutions 4.1 Integrated color registration system 4.1.1 Disadvantages of discrete chromatography:
For printing systems, the key lies in the overprinting accuracy of the chromatography system. The popular chromatography system solution currently on the market is a discrete design that is combined into a system by the supplier of the transmission system product and the supplier of the chromatography system. This has the following drawbacks:
The price is high, and the price of a professional color registration system is usually in the thousands of dollars.
Two or more suppliers need to solve the system failure.
4.1.2 advantages of integrated color registration:
B&R relied on the strong performance of its products and B&R's accumulation of industrial application software in the printing machinery field. It designed the solution of integrated color registration system, resulting in a subversive design of traditional solutions and huge cost savings. Moreover, the completion of the entire system by an independent supplier will not cause too much inconvenience in system maintenance and upgrades.
The reason why B&R is able to implement this system well is that it has the advantages of its own hardware. What's more important is that the software libraries accumulated in the industry have been brought into play.
4.1.3 Integrated color registration algorithm design The integrated color registration system inputs the deviation of each printing unit into the registration system model. This model is based on fuzzy control and is designed and modeled. The parameters include the printing related process parameters such as tension, temperature and friction coefficient. , printing length, speed, etc. Since the printing system is a continuous printing process, the deviation adjustment of any one unit will have an impact on other systems. Through the coupling and decoupling operations of the multivariable system, the system will give the adjustment amount to The motion control system and motion control system are adjusted in real time to maintain the high precision of printing.
Traditional PLC can't design such a complicated algorithm, but because PCC has high-level language programming ability, can carry on the software design of the algorithm relatively easily, and can support the development of the application program through a variety of open libraries.
4.2 Color code input directly to the driver ACOPOS servo driver is a modular design of the drive system, it has intelligent features, has its own strong processing capabilities, and its design is a multi-slot way, including communication, encoder and I /O total of four slots, usually the first slot for communication, such as CAN, POWERLINK, 2nd to 4th slot can be used for encoders can also be used for I / O, and even can be directly inserted into the CPU module In this application, the signal of the color mark sensor is directly sent to the ACOPOS driver. The signal sampling, filtering, processing, coding, and communication packages are completed in the driver, and then sent to the color registration system. This design has a faster response speed than the traditional one. The PLC+I/O module is faster.
4.3 Virtual Spindle Technology The virtual main shaft refers to the mathematical model established between the motion control axis and the axis, because the speed and position synchronization problems of all motion control can be attributed to the mathematical relationship between the servo axes. The virtual spindle does not refer to A specific axis, but the relationship between them, because it does not exist, but an ideal axis, then there is no wear and tear, there is no deviation, and other servo axes follow this virtual spindle With 1:1 electronic gear synchronization, the ACOPOS driver can support electronic gear synchronization accuracy of up to 32-bit resolution.
4.4EthernetPOWERLINK real-time communication technology Real-time communication is a key part of the system. Whether it is the uploading of deviation signals to the color registration system and the set adjustment of the chromatography system, and the electronic gear synchronization relationship between the motion control systems, it needs to pass through the high-speed data channel. Provides data exchange between axes.
In this system, the printing speed is up to 300m/min, and the precision requires +/-0.1mm. Each refresh cycle of color registration is completed within a few milliseconds. Usually, the communication refresh cycle is higher than such an order of magnitude to ensure high precision. Synchronization, and POWERLINK can achieve the fastest refresh cycle to 100uS, taking into account the driver's position loop, match system task cycle matching, usually set to 400uS or 800uS, fully meet the high-speed printing system's high real-time requirements.
POWERLINK is a 100Mbps, high-speed real-time Ethernet with jitter <<1uS. It can provide fast channels for a large number of data exchanges of the entire system, enabling the system to complete fast data exchange and ensure system synchronization accuracy.
5. Concluding remarks The integrated color registration system has almost eliminated the cost of the chromatography system compared to the original system. This is a huge cost saving for the machine manufacturer, and its competitiveness is self-evident. More importantly, the system has high running accuracy and saves paper. Because of the use of pre-printing technology, it only needs to complete rapid registration in just a few short paper transfers, and enters a stable operation phase, which can increase work efficiency and reduce Waste of paper.
In addition, the requirements for environmental protection in the beer and beverage industry are also more stringent. In order to reduce the harm to the human body in the production process, environmental protection printing is also paid more attention, which also makes flexographic printing gradually reflected its advantages over offset printing and gravure printing. .
1. System Requirements Width Flexo Printing Due to its high requirements on the precision of machined parts, wide-format flexo printing has not been vigorously developed for a long period of time. At present, this model is mainly used for The printing of corrugated paper is known as the “preprinting technique†using this printing process. In contrast, the printing after the production of corrugated cardboard is called the “postprinting technologyâ€. Compared with the postprinting technology, the printing is preprinted. Technology has its unique advantages:
Preprinting technology is efficient and of good quality. For the printing of corrugated board, the preprinting technology is to link the printed good paper with the corrugated line, and the cartons can be directly produced without the need to transfer to the slot printing machine like the post-printing technology. , And, it is different from the post-printing technology, it will not cause pressure on the corrugated paper, thereby affecting the strength of the corrugated box.
Environmental protection. Flexographic printing uses water-based inks, which are more environmentally friendly than oil-based inks, and have a smaller impact on the air and on the production floor.
Larger format. For a wide flexo, a 1200 mm to 2200 mm printed web can provide surface printing of large packaging containers, and can also provide printing of multiple products simultaneously by slitting.
The system required to achieve a printing speed of 300m/min, printing accuracy +/-0.1mm, width 1200mm.
2. Equipment composition and working principle The unit consists of unwinding, front traction unit, rear traction unit, printing color group (generally no more than 9 colors), and rewinding unit, as shown in Figure 1.
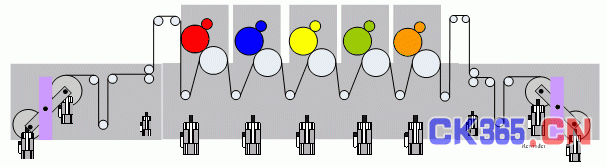
Figure 1 Equipment composition of a flexographic printing unit
2.1 Unwinding unit The unwinding section is mainly composed of an air brake and a tension swing roller. The material winding core is placed on the unwinding rack through the air expansion shaft. When the air brake brake air pressure is zero, the material roll and the air expansion shaft are together. Can be free to rotate; In normal work, by adjusting the air pressure (proportional valve: 0 ~ 10VDC represents the pressure from small to large) to adjust the braking force and control the unwinding tension, the specific working principle shown in Figure 2.
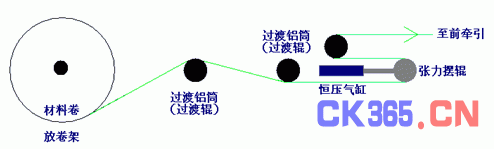
Figure 2 Working principle of unwinding unit
The tension roller keeps a constant thrust (the pressure in the cylinder is constant). In normal operation, we adjust the air pressure of the air brake through the PID so that the tension roller stays in the set position (the position of the tension roller is installed in the pendulum. The potentiometer on the roll detects it, 0~10V means, generally adjust the middle value to 5V), this maintains the constant tension of unwinding, which is also the first level of tension control before the material enters the printing.
2.2 Front traction part The front traction part is composed of front traction motor, front traction roller, front traction roller and a tension swing roller. The role of the front traction part is to send the printing material to the printing part with a constant tension. The working principle is shown in Figure 3.
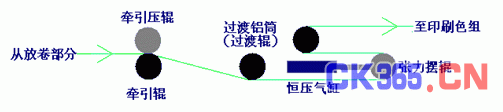
Fig. 3 Diagram of the working principle of the front traction part
The traction roller is driven by a traction motor, and the traction roller presses on the traction roller during normal operation to prevent the material from slipping. In normal operation, the PID adjusts the speed of the front traction motor to control the tension swing roller at the set position, thereby maintaining a constant material tension. This is the second level of tension control before the material enters the printing section. At the same time, the front pulling pressure roller also acts as a tension isolation, and the tension fluctuation of the unwinding portion can be isolated.
2.3 printing part of the printing part by the color group, 7 color is a 7 color group; each color group consists of color group motor, bottom roller, plate roller, ink roller composition. The color group motor drives the bottom roller through a gear box, and the plate roller, the bottom roller and the ink feeding roller are put together by gears. The principle of work is shown in Figure 4.
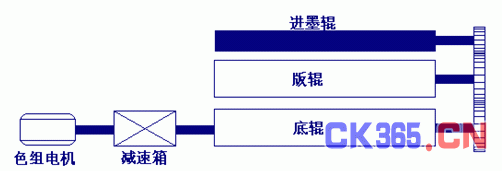
Figure 4 shows the working principle of the printing part
Plate rollers, bottom rollers, and ink inlet rollers are matched by gears to ensure consistent surface line speed; before starting printing, there is a gap between the plate roller and the bottom roller, and the plate roller is in the raised state. The surface and the printed material are not in contact. When the plate roller is lowered, the surface of the plate roller is kept in light contact with the surface of the substrate to be printed, and the contact pressure between the plate surface and the material can be adjusted according to the printed pattern effect. The down roller is the plate roller and the ink feed roller. The order of the plate roller is: Stop the ink roller for 2 seconds, then back off the plate roller, keep the plate roller back signal and the ink roller stop signal for 2 seconds. Then both signals are reset. In normal printing, all color groups printed are kept in strict position synchronization, and all color group calibrations are exactly the same. Between the color group and the color group, the heated portion of each color group is printed and heated by hot air; the hot air is sent out by the total blower; each color group has a heater, which is divided into fast heating and slow heating. There are two types of heating: heating wire and steam.
2.4 Rear traction part The rear traction part is composed of a rear traction motor, a rear traction roller, a rear traction roller and a tension swing roller; the function of the rear traction part is to bring the printing material out of the printing part with a constant tension. The working principle diagram is shown in Figure 5.
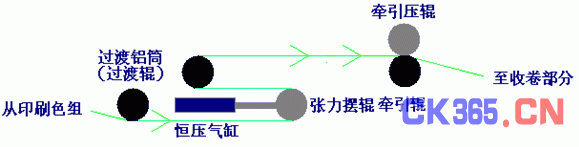
Figure 5 working principle of the rear traction part
The tension roller is installed between the last color group and the rear traction. Just like the front traction, during normal operation, the traction roller is also pressed on the traction roller to prevent the material from sliding, and at the same time, it plays the role of tension isolation; the system is based on the oscillating roller. The setting position of the traction motor is regulated by the speed of the PID to stabilize the swing roller at the set position so as to stabilize the rear traction tension.
2.5 The winding part of the flexographic printing press adopts the surface friction winding method. The winding part is mainly composed of a tension swing roller, a friction roller, and a passive air expansion shaft. Its working principle diagram is shown as in Fig. 6.
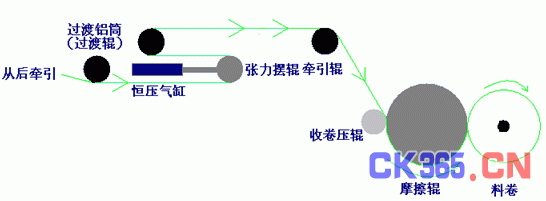
Figure 6 working principle of the winding part
The friction roller is driven by a third-party asynchronous motor. The motor is driven by ACOPOS or vector inverter. During normal operation, the take-up roller presses the material on the friction roller surface, and the take-up roller also presses on the friction roller surface; the system passes tension. Comparison of the setting position and actual position of the pendulum roller The speed of the friction roller drive motor is adjusted by the PID, and the tension roller is controlled to stabilize at the set position to achieve constant tension winding. The friction roller and the pressure roller are soft rubber rollers.
3. Control System Hardware Configuration The hardware configuration of the system is shown in Figure 7. It is mainly composed of a PowerPanel - man-machine interface with integrated control, display and operation, multiple ACOPOS intelligent servo drives and EthernetPOWERLINK real-time communication Ethernet. constitute.
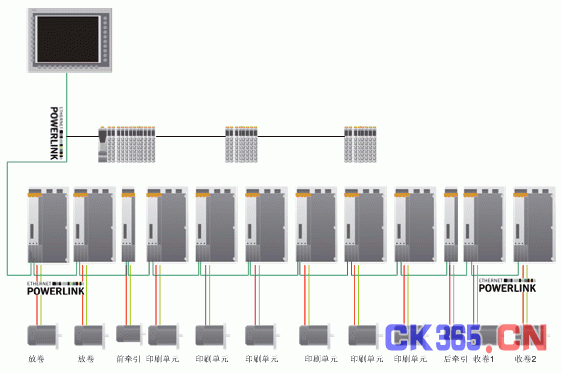
Figure 7 system hardware configuration
4. Key technologies and solutions 4.1 Integrated color registration system 4.1.1 Disadvantages of discrete chromatography:
For printing systems, the key lies in the overprinting accuracy of the chromatography system. The popular chromatography system solution currently on the market is a discrete design that is combined into a system by the supplier of the transmission system product and the supplier of the chromatography system. This has the following drawbacks:
The price is high, and the price of a professional color registration system is usually in the thousands of dollars.
Two or more suppliers need to solve the system failure.
4.1.2 advantages of integrated color registration:
B&R relied on the strong performance of its products and B&R's accumulation of industrial application software in the printing machinery field. It designed the solution of integrated color registration system, resulting in a subversive design of traditional solutions and huge cost savings. Moreover, the completion of the entire system by an independent supplier will not cause too much inconvenience in system maintenance and upgrades.
The reason why B&R is able to implement this system well is that it has the advantages of its own hardware. What's more important is that the software libraries accumulated in the industry have been brought into play.
4.1.3 Integrated color registration algorithm design The integrated color registration system inputs the deviation of each printing unit into the registration system model. This model is based on fuzzy control and is designed and modeled. The parameters include the printing related process parameters such as tension, temperature and friction coefficient. , printing length, speed, etc. Since the printing system is a continuous printing process, the deviation adjustment of any one unit will have an impact on other systems. Through the coupling and decoupling operations of the multivariable system, the system will give the adjustment amount to The motion control system and motion control system are adjusted in real time to maintain the high precision of printing.
Traditional PLC can't design such a complicated algorithm, but because PCC has high-level language programming ability, can carry on the software design of the algorithm relatively easily, and can support the development of the application program through a variety of open libraries.
4.2 Color code input directly to the driver ACOPOS servo driver is a modular design of the drive system, it has intelligent features, has its own strong processing capabilities, and its design is a multi-slot way, including communication, encoder and I /O total of four slots, usually the first slot for communication, such as CAN, POWERLINK, 2nd to 4th slot can be used for encoders can also be used for I / O, and even can be directly inserted into the CPU module In this application, the signal of the color mark sensor is directly sent to the ACOPOS driver. The signal sampling, filtering, processing, coding, and communication packages are completed in the driver, and then sent to the color registration system. This design has a faster response speed than the traditional one. The PLC+I/O module is faster.
4.3 Virtual Spindle Technology The virtual main shaft refers to the mathematical model established between the motion control axis and the axis, because the speed and position synchronization problems of all motion control can be attributed to the mathematical relationship between the servo axes. The virtual spindle does not refer to A specific axis, but the relationship between them, because it does not exist, but an ideal axis, then there is no wear and tear, there is no deviation, and other servo axes follow this virtual spindle With 1:1 electronic gear synchronization, the ACOPOS driver can support electronic gear synchronization accuracy of up to 32-bit resolution.
4.4EthernetPOWERLINK real-time communication technology Real-time communication is a key part of the system. Whether it is the uploading of deviation signals to the color registration system and the set adjustment of the chromatography system, and the electronic gear synchronization relationship between the motion control systems, it needs to pass through the high-speed data channel. Provides data exchange between axes.
In this system, the printing speed is up to 300m/min, and the precision requires +/-0.1mm. Each refresh cycle of color registration is completed within a few milliseconds. Usually, the communication refresh cycle is higher than such an order of magnitude to ensure high precision. Synchronization, and POWERLINK can achieve the fastest refresh cycle to 100uS, taking into account the driver's position loop, match system task cycle matching, usually set to 400uS or 800uS, fully meet the high-speed printing system's high real-time requirements.
POWERLINK is a 100Mbps, high-speed real-time Ethernet with jitter <<1uS. It can provide fast channels for a large number of data exchanges of the entire system, enabling the system to complete fast data exchange and ensure system synchronization accuracy.
5. Concluding remarks The integrated color registration system has almost eliminated the cost of the chromatography system compared to the original system. This is a huge cost saving for the machine manufacturer, and its competitiveness is self-evident. More importantly, the system has high running accuracy and saves paper. Because of the use of pre-printing technology, it only needs to complete rapid registration in just a few short paper transfers, and enters a stable operation phase, which can increase work efficiency and reduce Waste of paper.
Machinery And Equipment Parts,Metal Pipe Clips,Metal Tube Clamp,Clamp Metal
Ningbo Metal Sharing Supply Chain Management Co., Ltd , https://www.zenlesf.com